Optimizing processes, enhancing efficiency and inspiring customers: Semperit relies on operational excellence and thus on a corporate culture that promotes excellence. About a global success model for continuous improvement.
Employee suggestion program. Using this cumbersome term, Semperit was improving operational excellence in the company as early as in the 1980s – on the initiative of employees. And at the time even regularly received awards for its achievements from the Austrian Federal Ministry of Trade, later the Federal Ministry of Economic Affairs (see figure). Today, the focus in this area is still on optimally aligning processes, systems and resources to achieve sustainable excellence, or as Stephanie Rechberger, who heads the Operational Excellence department at Semperit, puts it: “It’s not just about efficiency or eliminating waste in the value chain. Above all, it is about creating a culture of improvement in the company that promotes excellence in all areas. Our employees work every day on how they can further improve processes. Even small adjustments – two or three steps less – have a big impact when repeated thousands of times worldwide.”
Facts and figures
At the heart of the Operational Excellence program is a global platform where all Semperit sites can enter their suggestions for improvement. The production managers evaluate these ideas, and for more complex projects, Stephanie Rechberger’s team of four gets involved. They analyze data, prepare evaluations, exchange ideas across disciplines and engage in the targeted sharing of best practice. It is about facts and figures, the area that Rechberger has been passionate about since her student days at the University of Leoben: “The fact that I can learn so many new things and broaden my horizons through structured work and problem analysis fascinates me time and again. It allows me to develop personally.” This is one of the reasons why Rechberger has been working at Semperit for more than 15 years.
Focus on sustainability
ESG issues account for an ever-greater share of operational excellence. “A project that leads to the continuous improvement of production processes must also be sustainable. Otherwise, it’s pointless,” Rechberger emphasizes. In the areas of waste reduction, resource conservation and energy efficiency, a great deal has been achieved in recent years – in Wimpassing as well as in the hose production plant in Odry, Czech Republic, which serves as a role model for the group. Site manager Daniel Pazdirek says: “It’s clear that once you’ve achieved a lot, it becomes increasingly difficult to set up new projects. But there is no such thing as 100 percent perfection. There is always something that can be improved.”
Ultimately, operational excellence is about customer satisfaction. “We not only have to ensure that our customers receive their delivery in the desired quality, on time and at a fair price. We also have to keep surpassing ourselves to remain or become best in class. And that can only be achieved by constantly improving our processes,” says Rechberger, getting to the heart of the matter.
„We have to keep surpassing ourselves to remain or become best in class.”
Stephanie Rechberger, Head of Operational Excellence
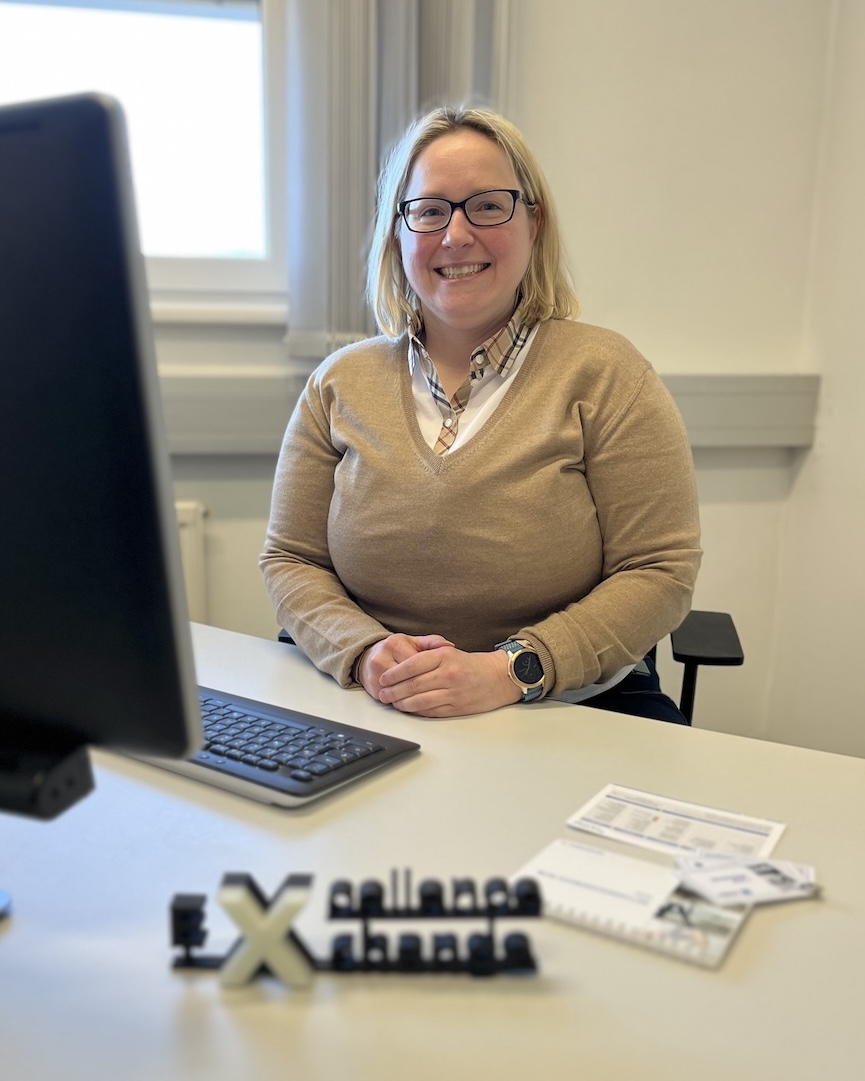